干法制粒工艺因无需溶剂、能耗低等优势被广泛应用于制药、食品、化工等领域,但颗粒粒径分布不均的问题常导致产品流动性差、压片困难等后果。
一、颗粒不均的成因分析
1.原料特性不达标
粒径分布差异大:原料粉末的原始粒径差异显著(如D50值波动>20%),导致预压成型时细粉填充不足,粗颗粒难以破碎。
流动性差:原料休止角>40°时,进料不均匀,辊轮压力分布失衡,颗粒致密度差异增大。
湿度控制不当:原料含水量<1%时粘合力不足,颗粒松散;>3%时易粘连结块,压制后形成硬块与细粉并存。
2.设备参数设置不合理
辊轮间隙与压力失衡:间隙过小(如<0.3mm)导致过度挤压,颗粒硬度过高且易破碎;间隙过大(>1.0mm)则成型率低,产生大量细粉。
送料速度波动:螺旋送料器转速不稳(±10%以上)导致供料密度不均,辊压区受力不一致。
破碎刀磨损或角度偏差:刀片钝化或安装角度>15°时,颗粒二次破碎不充分,粗颗粒残留率增加。
3.工艺条件适配性不足
预压阶段压力不均:预压压力低于30MPa时,粉末未充分密实,颗粒内部孔隙率高,易碎裂。
压制时间过短:单次压制时间<2秒时,粉末未融合,颗粒表面粗糙度增加。
温度控制失效:辊轮表面温度波动>±5℃,导致物料热塑性变化,局部粘合性能差异。
二、系统性解决策略
1.原料预处理优化
分级过筛:采用振动筛(80~120目)去除超细粉(<50μm)和粗颗粒(>500μm),控制原料D90/D10<5。
添加助流剂:引入0.5%~1%微粉硅胶或硬脂酸镁,降低休止角至30°以下,提升进料均匀性。
精准控湿:通过流化床干燥或加湿系统,将原料含水量稳定在1.5%~2.5%区间。
2.设备参数精细调控
动态调整辊轮间隙:根据原料特性设定初始间隙(0.5~0.8mm),并安装压力传感器实时反馈调节,误差控制在±0.05mm内。
变频稳速送料:采用伺服电机驱动送料螺旋,转速波动率<2%,确保供料密度一致。
定期维护破碎系统:每生产200批次后更换刀片,调整刀片与筛网间隙至0.1~0.3mm,粗颗粒残留率可降至<3%。
3.工艺参数智能适配
阶梯式压力加载:预压阶段分两级加压(20MPa→35MPa),延长密实时间至3秒,颗粒孔隙率降低至15%以下。
温度闭环控制:在辊轮内部嵌入热电偶,通过PID算法维持表面温度在45±2℃(适用于热敏性物料)。
在线粒径监测:集成激光粒度仪实时检测颗粒分布,自动反馈调整破碎机转速。
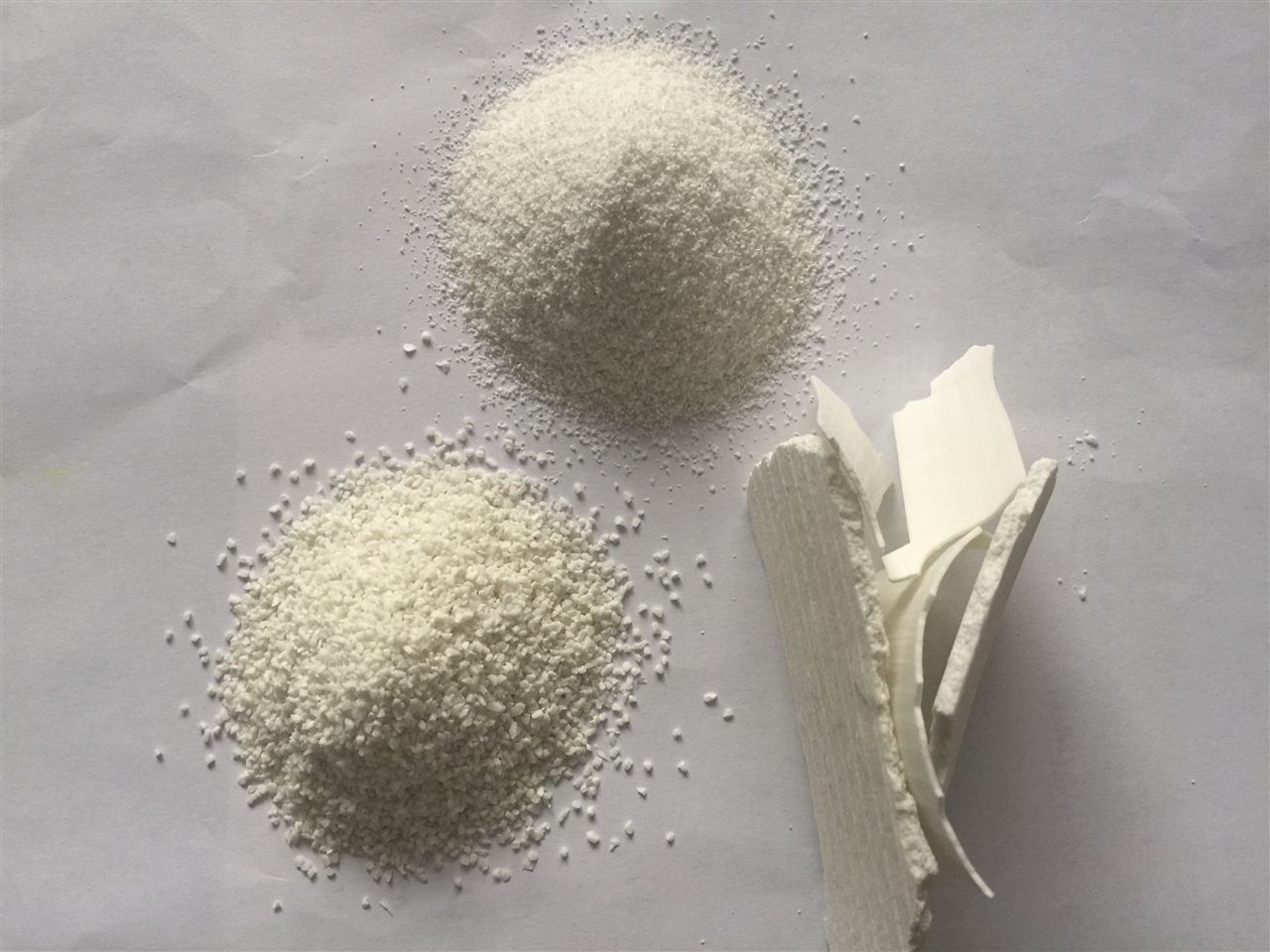